聚乙烯接口皮子是一种广泛应用于塑料管道系统中的连接部件,主要用于确保不同管道之间的牢固连接,避免泄漏,并提高系统的使用寿命。其制造工艺与技术直接影响到性能和使用效果,本文将对其制造工艺进行解析。
聚乙烯接口皮子的制造过程一般包括材料选择、模具设计、注塑成型、焊接处理等几个关键环节。
一、材料选择
原材料通常采用高密度聚乙烯(贬顿笔贰),因其具备良好的抗压、抗腐蚀、耐磨损等特性。此外,高密度聚乙烯具有较高的机械强度和较低的线膨胀系数,使得其在较大温度变化和压力条件下能够保持稳定性能。
二、模具设计
在制造时,首先需要根据设计要求进行模具的设计。模具设计要求具有良好的流动性,能够使聚乙烯材料在加热和注射的过程中均匀填充到模腔内,确保产物的尺寸精度与质量。
叁、注塑成型
注塑成型是制造聚乙烯接口皮子最常见的方式。该工艺包括加热、注射、冷却等步骤。具体流程如下:
1、加热:聚乙烯颗粒被加热至熔融状态,此时,聚乙烯的粘度降低,具备了流动性。
2、注射:将熔融后的聚乙烯通过注射机的喷嘴注入模具中,模具内的形状会决定最终外形和尺寸。
3、冷却:聚乙烯在模具中冷却后固化,形成所需的形态。冷却时间需要根据模具的尺寸、聚乙烯的冷却速率等因素进行合理控制。
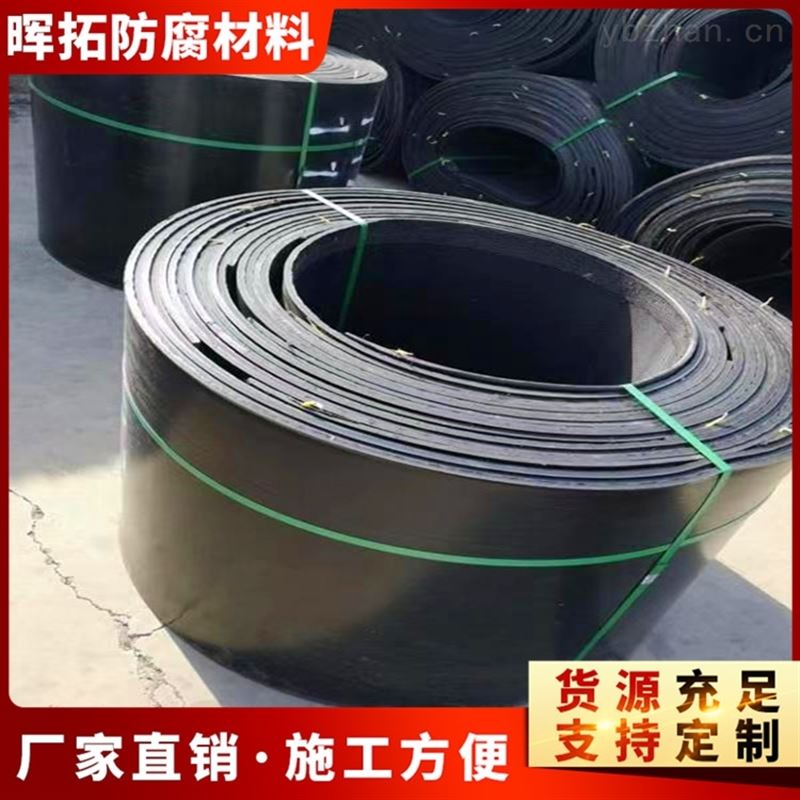
四、焊接与组装
完成注塑成型后的通常还需要进行后续的焊接或组装,以确保各部件之间的牢固连接。最常见的焊接技术包括热熔焊接和电熔焊接。
1、热熔焊接:通过加热接头部分,使聚乙烯材料达到熔融状态,然后将两端的管道接口皮子进行对接,冷却后形成稳定的连接。该工艺广泛应用于中小型聚乙烯管道的连接。
2、电熔焊接:采用电熔接头,通过通电加热金属丝,使接头处的聚乙烯材料熔化,达到连接目的。该工艺适用于较大尺寸和高压力环境下的管道连接。
聚乙烯接口皮子的制造工艺涵盖了从原材料选择、模具设计到注塑成型及焊接处理等多个环节。通过不断优化这些工艺,能够生产出质量更高、性能更优的产物,为管道系统的安全运行提供保障。